Aircraft Industry
Kayco Spray Booths Case Study
Case Study Aircraft Industry
Over the years, Kayco Spray Booths positioned itself to fulfill demanding requests of aerospace manufacturers.To showcase our expertise and know-how in this exciting industry, we will highlight some interesting features of a project we completed for Sikorsky Aircraft.
Sikorsky Support Services needed to increase their aircraft maintenance capacity in Beeville, Texas. Manufacturing spray booths for aircraft comes with some interesting challenges which Kayco Spray Booths can address successfully.
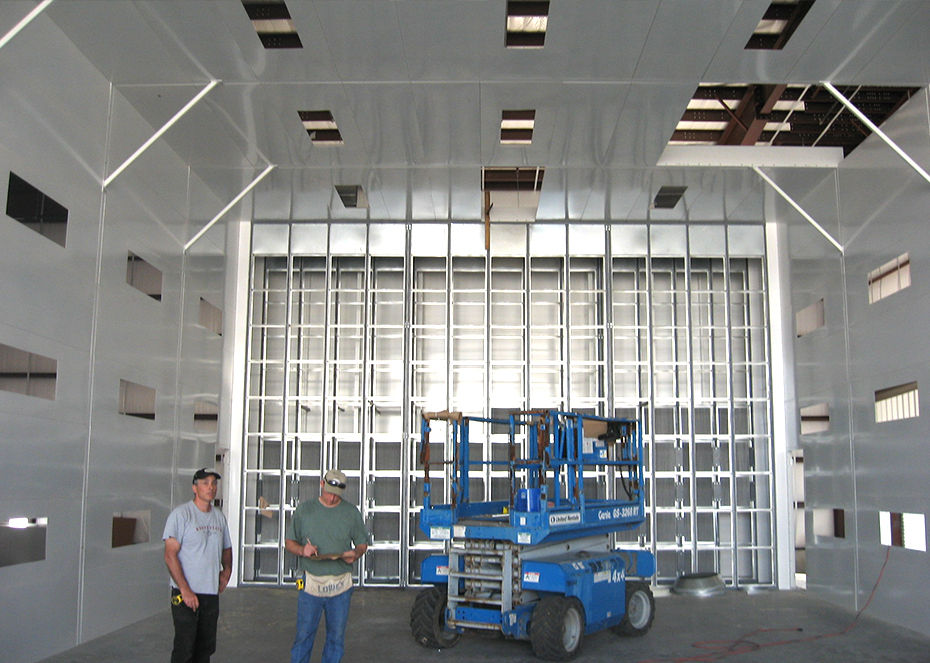
Size, Scalability, Stability & Comfort
Fitting an entire helicopter fuselage into a spray booth required us to build a booth with an internal dimension of 30’W X 20’H x 80’L. To accommodate even larger aircraft in the future, its width can easily be increased to 45 feet. The booth is designed to always carry its weight without depending on support from an external building structure.
Special consideration is given to sound attenuation such that sound pressure levels never exceed 85 dBA in the spray booth.
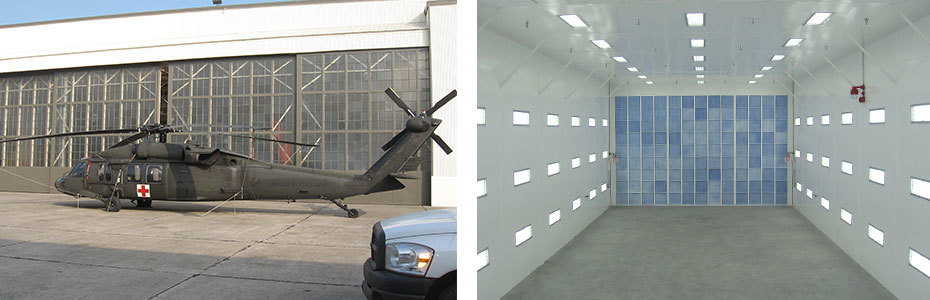
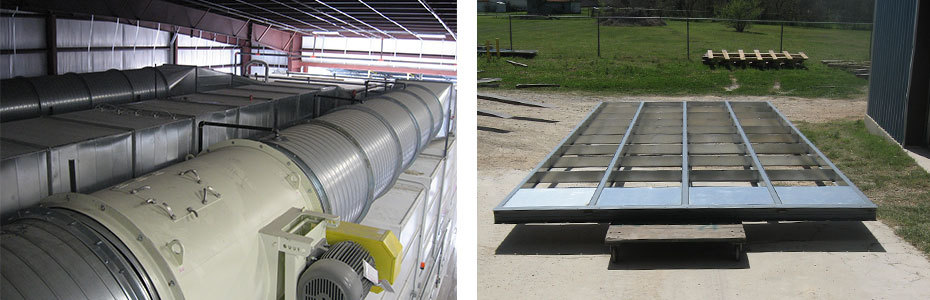
Reduced Maintenance Cost
Air Filter Optimization
Replacing fewer filters less often helps reduce the maintenance cost of our booth. As opposed to conventional practice, Kayco decided against the use of standard drop-in panel filters by using larger custom filters which expose fewer edges and increase the filter area.
Air Velocity Control
Balancing airflow within a spray booth is of utmost importance. A high inlet air velocity may cause an unwanted venturi effect which could cause unintended diffusion of paint particles within the spray booth. Thus, Kayco Spray Booths designed a custom supply air plenum that allows an inlet air velocity of no more than 1,000 feet per minute.
Control Panel Integration & Online Monitoring
Off Site Monitoring
The booth is equipped with latest sensor technology to monitor a broad array of system metrics at any given time. The control panel (PLC) allows for an online connection, enabling our system specialists to troubleshoot incidents remotely, which reduces the maintenance cost of our unit significantly. Furthermore, potential problems can be detected as early as possible. The system is capable of recording and maintaining at least 500 historical data points.
Reduced Energy Consumption
80% Exhaust Recirculation and Climate Control
Hot air temperatures increase the productivity of the spray booth since paint dries quicker in hot air. However, Kayco has to consider other temperature and humidity requirements when it comes to painting aircraft, and because true climate control is often required, implementing an 80% recirculation design not only represents significant reductions to on-going operating cost but it can reduce initial capital expenditures as well. Recirculation designs include continuous monitoring of the LEL (lower explosive limit) to ensure safe operating conditions. A Makeup Air Unit ensures a temperature of 140 degrees Fahrenheit in drying mode.
The spray booth observes temperature and humidity limits due to climate-sensitive electronics housed within aircraft.
Fire Safety
The equipment and installation meet Sikorsky EH&S and Fire Department requirements as well as FM Global Standards and Regulations.
Exhaust Air Filtration
The multistage primary dry air filtering exhaust system meets the requirements for the US Aerospace Manufacturing and Rework facilities NESHAP – MACT regulations.